No Compromises. Speed, Density and Sequencing Power This Next Generation, Automated Order Fulfillment Cube.
Compress warehouse functions from receiving to shipping, into a scalable, high-speed, space and cost-efficient system - for goods of nearly any size, shape, and temperature environment.
Imagine an AS/RS system that doesn’t just store and retrieve but also sorts, buffers, stages, and sequences full cases, bulky items, and each picks—all within a single, compact, and efficient cube. Freespace Robotics revolutionizes warehouse operations by consolidating and automating functions traditionally performed externally by conveyors, forklifts, and manual labor, all while requiring less floor space.
Unlike conventional AS/RS systems focused primarily on storage and retrieval, Freespace’s dynamic deep-lane rack design integrates sorting, pre-staging, and sequencing directly into the cube. This eliminates the need for external conveyors and processes, delivering orders in sequence to pick stations or docks.
The result? Significant savings in capital, time, labor, and space.
Scale As You Need
The modular rack design, which expands vertically and horizontally like Lego blocks, adapts to any future demands, product changes, business requirements and capacity expansion. With the flexibility Freespace Robotics offers in terms of size and weight of goods handled, and the open-ended structural options, we’ve attracted leaders in retail, defense logistics, wholesale food distributors and grocery, as well as parts suppliers and manufacturers to our solution. With no height limitations and the ability to extend an installed system later, Freespace offers a versatile solution that grows and adapts to your business - extending its performance and ROI.
'EcoShuffle' Storing & Retrieving
The core of our breakthroughs in speed, flexibility, reliability, versatility and cost efficiencies is how the system moves goods. Our robotic carrier pairs, approach two rows simultaneously and shuffle goods in an energy efficient manner – clockwise or counterclockwise to the nearest exit, depending on the fastest path to retrieve goods.
Fit Your Warehouse
Not all warehouses are shiny new buildings with perfect floors and out of the way walls and columns. We designed our system to accommodate the quirks of brownfield sites so that automation of cross-docking operations and 'goods to person' are accessible without a 7-figure renovation or 8-figure facility build. Our system, because of its structural design principles, can go around corners or columns, uneven roof lines and ductwork as well as adjust pitch and level for uneven flooring.
Fit Your Products
One of the challenges retailers, suppliers and distributors have trying to automate operations, is that the goods they carry come in such a broad range of sizes. Freespace Robotics system is the only solution that can automate piece-pick, bulky items and case-pick in the same system. Each layer of our AS/RS can be a different height, configured for different throughput rates and do so in vastly different dimensions. We don’t ask our customers to adapt their needs to the specs of our robots, we shape our carrier robots and configurations to meet the inventory automation needs of our customers.
Custom Applications
Because of our unique design, the Freespace Robotics system has the potential to revolutionize a number of new applications. Without needing robots to move on a floor, the Freespace design can be a powerful sequencing and 'goods to person' tool in a truck trailer, relieving the driver of multiple trips up and down the ramp and of having to find ordered items among the mixed pallets spread through the trailer. Additionally, the system can be suspended from ceilings to provide ASRS capabilities in small spaces, turning retail locations and grocery stores into micro-fulfillment centers.
Our Design Principles make this system like no other
Versatility Advantage
- Slot, store, retrieve, sort, stage, buffer and sequence in cube
- Modular structure adapts, expands to meet changing needs
- Goods to Person and Cross docking applications
- Robots move, store or retrieve more than one tote at a time
- Robots and components are outside the structure
- Additional robots do not create additional congestion
- Items can be stored and retrieved in a single trip
Operational Advantage
- As fast and dense - yet more versatile, than leading automated solutions
- Cube is accessible from more than one side
- Up to 100 pounds of case, each or bulky goods
- Turnkey software or easy integration with popular WMS systems
- Simple parts, simple movement, simple power, simple repair
- Robots and components are outside the structure
- No reliance on difficult to source and costly to recycle batteries
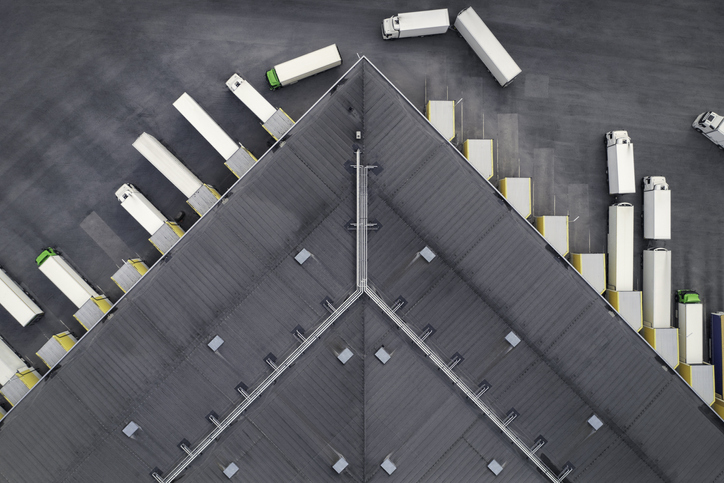
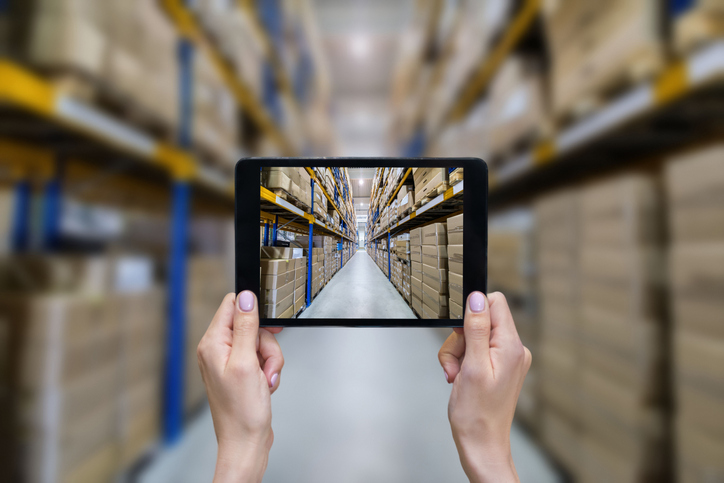
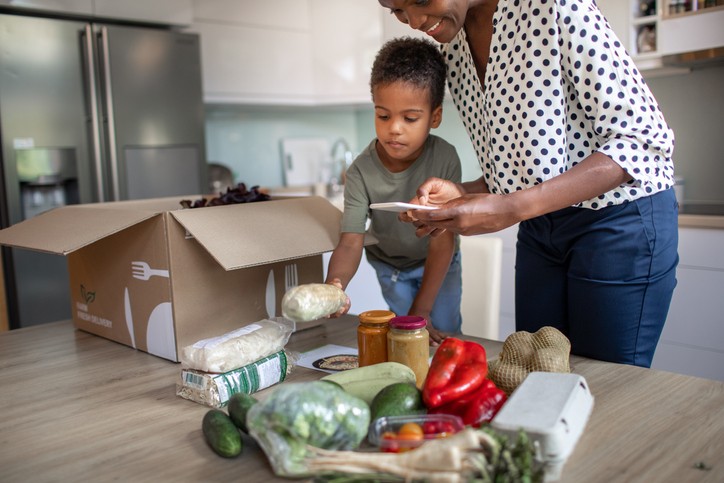
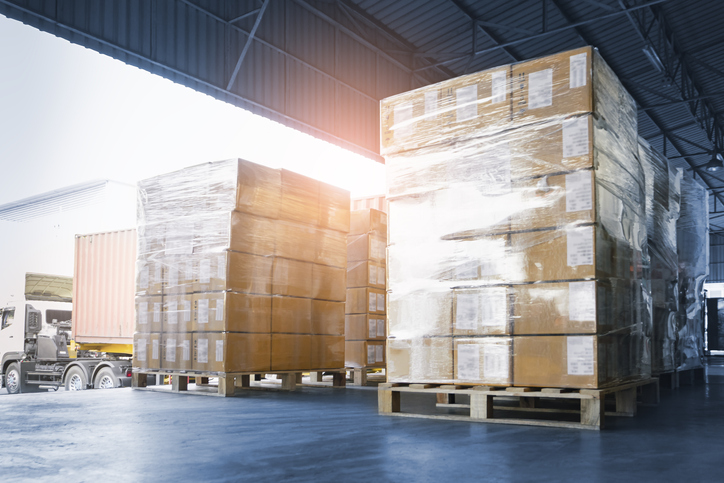
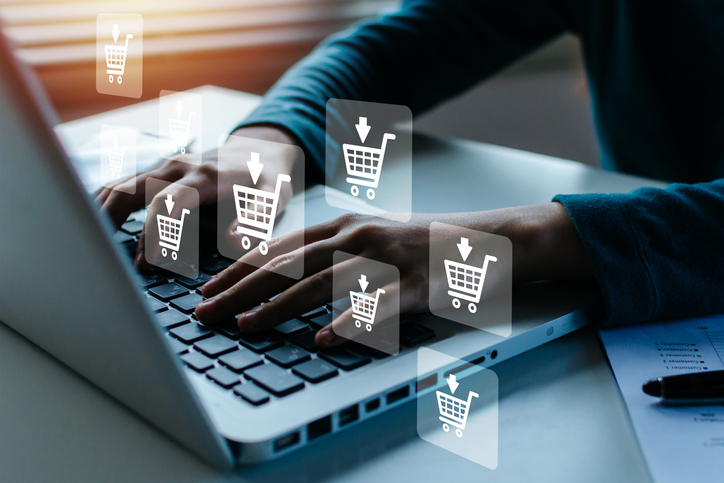
Freespace Robotics is American owned and operated, and our products are designed and made in America. Our headquarters, workshop facility and demonstration center are housed at the National Robotic Engineering Center (NREC) in the Robotics Row section of Pittsburgh, Pennsylvania. NREC, an independent unit of the famed Robotics Institute at Carnegie Mellon University, is a world leader in the applied development of automation, robotics and AI solutions for Fortune 500 companies, DARPA and DoD.
We understand the complexities of today’s fast-paced and rapidly changing supply chain environment. Businesses demand solutions that are not only high performance, cost-effective, more efficient - but also reliable and resilient amid economic fluctuations and labor shortages. We minimize international trade concerns with US-based sourcing, including US Steel at the materials core. This means that some Freespace Robotics solutions will be ready in as little as 6-8 months from concept to commissioning.
We aim to give warehouse and supply chain managers greater choices in customizing solutions for their unique operations. Our modular rack design means managers can, over time, automate some or all of their warehouse operations - in a single cube. Our design alleviates the need for costly mezzanines and sequencing conveyance to move goods to the dock in order. Our expanded tray sizes and weight limits means managers can automate most, if not all, of their inventory and not need separate areas to hold non-conveyables. Ideal for greenfield and brownfield locations alike, with high ROI and efficiency value propositions for;
- Warehouses and Distribution centers
- Fulfillment, Micro-fulfillment
- E-commerce, Grocery, Apparel, Manufacturing
- 3PL, Wholesale Food, Beverage and others with multi-stop delivery
- Defense Logistics, Kitting